Project Background
Currently, the facility is facing an extremely negatively pressured space at over 377,000 cfm exhaust, causing a number of safety issues for employees while opening and closing exterior doors. Sæplast currently operates two natural gas fired rotating molding ovens, a Ferry 400 Rotospeed and Orme 286 Rotospeed, to produce plastic insulated containers. There are several manually operated roof exhaust fans mounted close to the ovens and in other areas of the plant. The hot air that is created by the ovens during the production cycle is released into the atmosphere through the exhaust fans, wasting thermal energy. The plant is heated with ceiling-mounted natural gas fired radiant heaters.
Goals
- Design an air handling unit that captures the exhaust from the ovens
- Introduce fresh air into the production spaces
- Design a system that corrects the negative pressurization issues
- Design a system that lowers energy consumption while improving safety and efficiency
Design
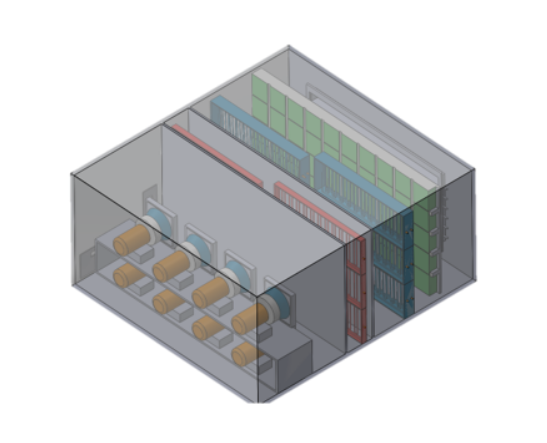
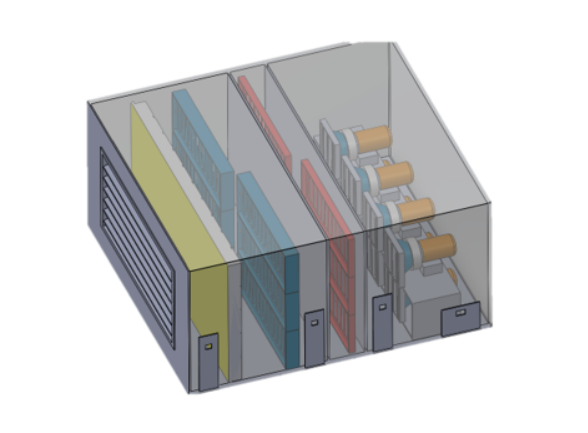
The design team’s detailed design recommendation includes one Outdoor Make-Up Air Handling Unit with variable recirculation return air with integrated heat recovery heating coil, one outdoor packaged air-cooled chiller, six natural-gas fired humidifiers with custom integrated humidification distribution manifold, two stages of air filtration, and eight supply fans with separate variable frequency drives as shown the images above. The heat recovery heating coil will be installed in the EF-10 exhaust air duct from the Ferry oven pre-cooling hood and include piping, insulation, valves, pumps, thermal fluid storage tank, and PLC controls components, connected to an integrated heating coil in the outdoor AHU.
These provisions make it possible to extract sensible heat from the exhaust air during mild shoulder season weather when a decreased amount of heat will be required in the production facility. The chilled glycol cooling coil will be integrated into the outdoor AHU and include piping, insulation, valves, pumps, thermal fluid storage tank, and PLC controls components, connected to an outdoor packaged air-cooled chiller. With the warm exhaust air recirculated in the facility and with the introduction of outdoor air into the AHU, the production space pressurization will be improved and have significantly less infiltration as a result, leading to a more comfortable and safer environment for employees. The major mechanical equipment has been configured outdoors in the Southwest corner of the Sæplast facility, integrating into the daily operations with minimal disruption in workflow.