Company Overview
PEI Bag Company was originally founded to meet the needs of the PEI potato industry, providing custom burlap bags. They have altered their business to now manufacture bags for industries including agriculture,fishing, food, and construction.
Problem Statement
The project being proposed is to automate the material handling processes currently required to support the Eco Man bag production line.
The Green Bag Packagers had to follow specific design requirements giving by PEI Bag Company:
- The production line must be staffable by three or fewer employees.
- A minimum throughput of 110 bags/minute.
- A payback period of less than three years for PEI Bag Company.
- It must bundle 6 and 15 bages per throughput.
- No overall increase in scrape rate of the bag.
- Setup time less than 10 minutes.
Current Process
The machine for manufacturing paper bags uses one operator and two workers to fully complete the manufacturing of the bag. These bags exit on a conveyor belt at a rate of 110 bags per minute. The bags are then inspected by a quality control worker.
The Eco-man line takes a total of six workers to complete this process. Thus, when the Eco-Man Bags are being produced, another production line must be shut down to account for the three extra workers required. This means for every day the Eco-Man Bag is produced, a day’s production is lost on another line.
The process is more complicated as the bags are moved to a table and sorted into groups of 6 or 15 bags. The grouped bags are arranged so that every 3 or 5 bags (depending on the bundle size) are rotated 180 degrees. This process requires two workers to keep up with the production rate of 110 bags per minute. Other workers are needed for Banding and storing the bags.
This left Jesse Cameron, Christian Wiedemer, Javon Mayhew, and Rob Smith of Green Bag Packagers quite the problem to solve…
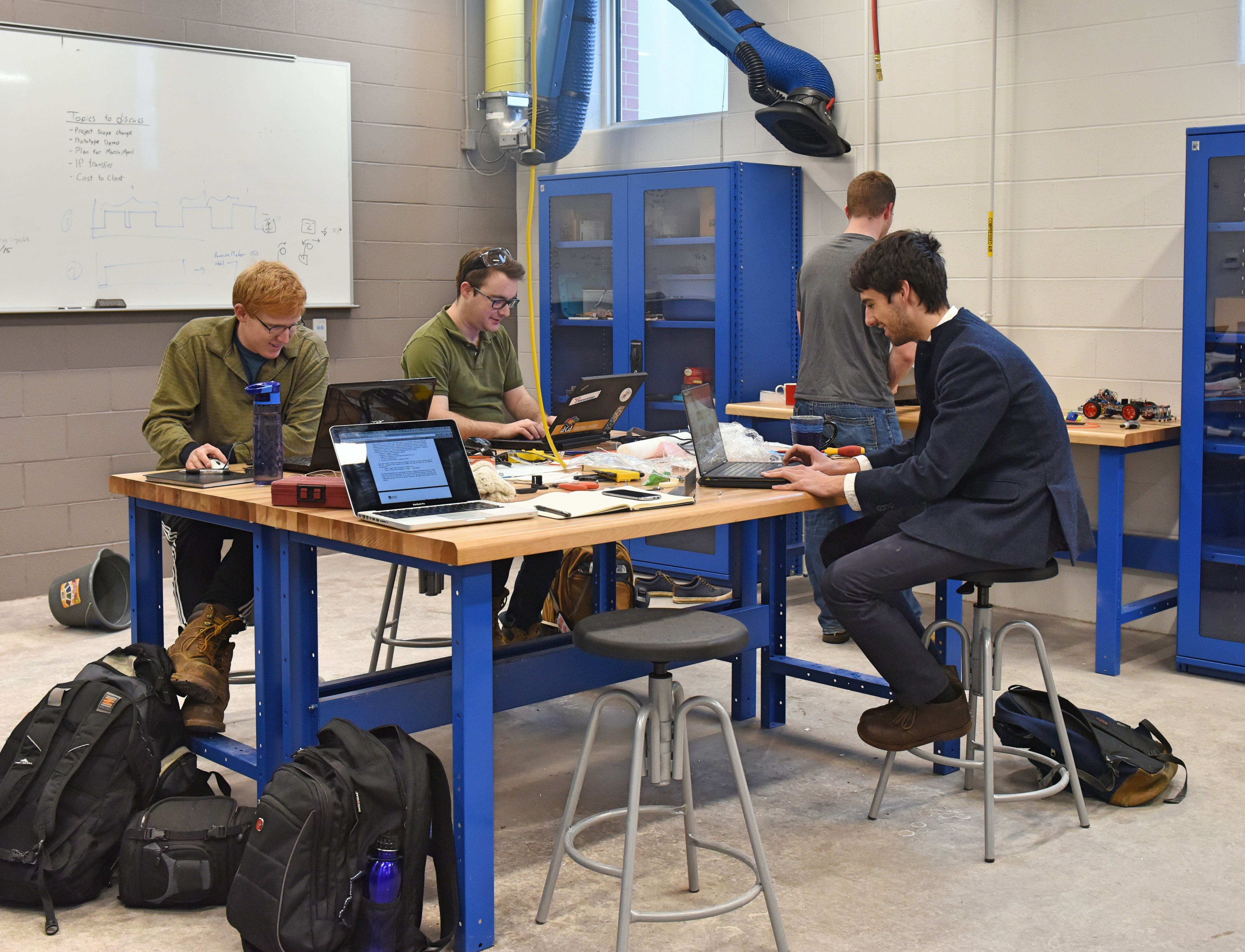
Green Bag Packagers working in their Project Bay
The team started with a mechatronics system that would automatically stack and band paper bags
Final Design CAD Prototype
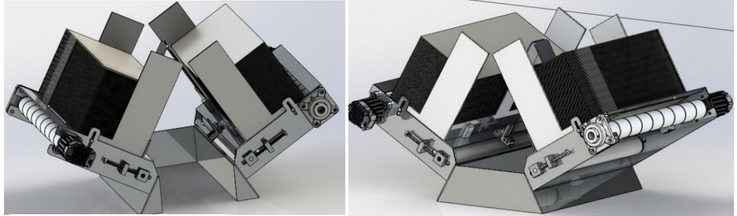
Final Design Assembly
Overhead View of Prototype
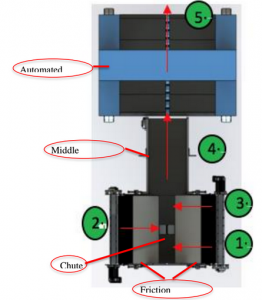
Overhead View Of the Final Design Assembly
The first problem the team encountered from the first design was that their friction feeder needed side adjustments for the bags to flow smoothly. The major design changes consist of the implementation of adjustability into the design for testing purposes. From product testing, the hopper design has also been altered in a manner to better control the bags out of the feeder.
Solution
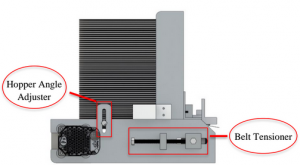
Side Adjustments
The second problem originated from the bags becoming “twisted” once coming into contact with the belt. This is believed to occur from the thinner end of the bag coming into contact with the belt before the thicker end cause a rotation of the bag. Once rotated, the bags would get stuck on the sides of the feeder.
Solution and Final Feeder Design
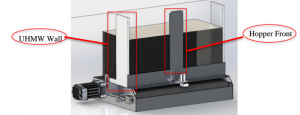
This CAD shows the final design of the Friction feed, with a new ‘Ultra High Molecular Weight (UHMW) wall that will keep the bags from shifting left and right as they go through the feeder.
Project Outcome
The current weber machine runs at 110 bags/min. The new bander can make up to 30 bags/min, which is faster than the current weber machine. This bander is capable of 30 bands/min, which in turn is 180 bags/min for a bundle of 6 Eco-man bags and 450 bags/min for the bundles of 15. With the middle bander and conveyor, the line can operate with the desired three workers instead of six.
The drive motors are connected to relays and will stop on the push of the E-stop to ensure the safety of the employees.
The current prototype works as a proof of concept, but requires further tuning before it can be implemented at PEI Bag Company.